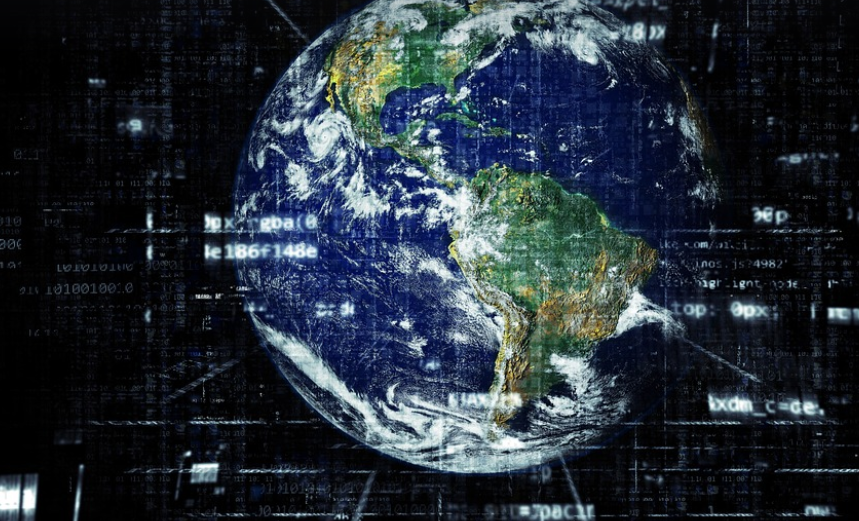
The Ever-Evolving World of Engineering Materials
Engineering materials are the backbone of our modern world, powering everything from skyscrapers to smartphones. Their durability, strength, and versatility are essential for countless applications across diverse industries. But how do we go beyond creating these materials and transform them into functional parts for real-world use? This is where manufacturing processes come in – a dynamic field that constantly pushes the boundaries of material science.
The sixth edition of “Manufacturing Processes for Engineering Materials” delves deep into this fascinating realm, offering a comprehensive guide to the techniques and technologies used to craft these essential materials. From traditional methods like casting and forging to cutting-edge processes utilizing advanced machinery, this book offers a holistic perspective on how we shape our world.
In this blog post, we’re going to explore some key principles and aspects of manufacturing that are central to the sixth edition’s content. We’ll cover everything from the fundamental steps involved in transforming raw materials into finished products to the unique challenges posed by different material types and their specific processing needs.
The Journey from Raw Material to Refined Product
The journey of an engineering material, starting with its raw form, is a complex one. It involves several phases that are crucial for achieving desirable properties in the final product. The first step often involves extracting or sourcing the raw material – be it iron ore for steel, aluminum from bauxite, or even polymers from petroleum.
Next comes the process of refining the raw materials to remove impurities and achieve a desired purity level. This can involve processes like smelting for metals, leaching for minerals, or purification techniques for specific chemicals. The quality of the initial material directly impacts the final product’s performance and longevity.
Shaping the Material: Key Manufacturing Processes
Once the material is refined, the real transformation begins – the molding process takes center stage. This involves shaping the material into its final form using various techniques:
* **Casting:** One of the oldest and most fundamental methods, casting uses molds to cast molten metal (like steel) or liquid polymers into specific shapes. From intricate engine components to large castings for industrial machinery, this method reigns supreme in many fields. * **Forging:** Applying heat and pressure to a material to reshape it is the core principle of forging. This can involve techniques like cold forging where tools hammer and shape metal under extreme pressures and temperatures, resulting in stronger and more durable materials. * **Rolling:** This process involves passing steel (or other metals) through rollers with different sizes and shapes to change their thickness and cross-section. This is a common method for producing long steel beams used in construction or sheets of aluminum for various applications. * **Extrusion:** A versatile technique where materials are forced through dies at high speed, creating consistent profiles and lengths. Common examples include pipes, wires, and other shaped sections, often used in industries like plumbing, electrical wiring, and automotive manufacturing.
The Future of Manufacturing: An Overview
While the traditional methods outlined above remain crucial, the field is continuously evolving. The sixth edition of “Manufacturing Processes for Engineering Materials” explores these advancements and their impact on the future of material processing:
* **Additive Manufacturing:** 3D printing, also known as additive manufacturing, has revolutionized the way we build objects. It allows us to layer materials precisely to create complex shapes with intricate details, previously unimaginable through traditional methods. This opens up exciting possibilities for rapid prototyping and customized solutions for various industries. * **Nanotechnology**: The manipulation of matter at the nanoscale is revolutionizing material science. Researchers are developing new nanomaterials with unique properties like high strength, conductivity, and even self-repairing capabilities. The sixth edition explores the potential of nanotechnology in reshaping manufacturing processes for future development.
As engineering materials continue to evolve alongside technological advancements, so too will our understanding of their production processes. The sixth edition promises a truly comprehensive look at this constantly changing world, offering insights into the technologies shaping the future of material science.
Beyond Material Properties: The Importance of Process Selection
Choosing the right manufacturing process isn’t just about selecting the best tool or method. It is about understanding the unique properties and characteristics of the material itself, as well as the desired end-product. This knowledge enables engineers to make informed decisions that optimize the process for specific applications.
Consider these factors: * **Material Properties:** The mechanical strength, thermal conductivity, or electrical resistance of a material heavily influence the best manufacturing process. For example, metals require heat treatment and shaping methods like forging or rolling, while polymers demand extrusion or injection molding techniques. * **Desired Product Form**: The final product’s form can further guide the selection. Is it a simple component with straight edges, like a bolt? Or is it a complex structure requiring intricate layering, as in 3D printing?
Choosing the right process requires careful analysis and consideration of these factors. The sixth edition’s comprehensive approach delves into these aspects, offering detailed information on different types of materials and their corresponding processing needs.