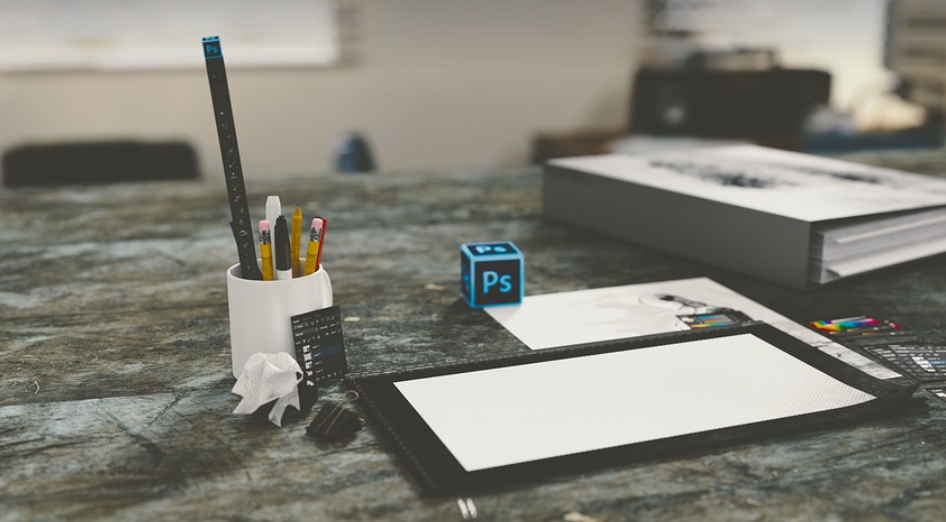
What are Stress and Strain?
Stress and strain are fundamental concepts in engineering, particularly in mechanics of materials. They describe the mechanical behavior of a material under load or applied force.
In simple terms, stress is the amount of force acting per unit area on a surface within a structural component. Think of it like pushing against a flat wall; the more you push, the greater the pressure you’re exerting on that wall. This is analogous to how stress works in objects!
Strain, on the other hand, measures the deformation or change in shape that happens under these forces. For example, if you push against that wall and it bends slightly, this bending is a form of strain.
The relationship between these two concepts is crucial for understanding how materials behave when subjected to loads. Stress and strain are interconnected; they’re like two sides of the same coin!
Engineering Stress: The “Standard”
Engineering stress, also known as “normal stress”, is a measure of the force per unit area acting on a material in a specific direction. We often think about it as pressure; it represents how much load is being applied.
The formula for engineering stress is straightforward:
Engineering Stress (σ) = Force (F) / Area (A)
It’s essentially the measure of force spread across a surface, which helps us understand how much pressure or weight is being put on a material.
Engineering stress is defined by an engineer’s perspective. They look at a standard set of rules and methods to define this “standard” form of stress. This is because it’s easier to compare materials and their behaviors under the same conditions, leading to more consistent results.
True Stress: The Real Deal
Now, let’s delve into true stress. It incorporates a crucial aspect that engineering stress doesn’t – the actual history of the load applied to a material. It considers the changes in strain across time.
True stress is calculated by dividing the **change in strain** (Δε) by the resulting **load change** (ΔF).
Here’s an equation that illustrates this:
True Stress (σt) = Δε / ΔF
Think of it this way: True stress is like understanding the actual changes in strain experienced by the material as load applies and then stops. It considers the whole picture, not just a snapshot.
Understanding true stress allows engineers to predict how materials will behave under more complex loading scenarios, which goes beyond basic stress calculations.
Why True Stress is Important
True stress provides a more accurate representation of how materials respond to real-world loads because it considers the history of the applied force. This is particularly important for materials that experience strain hardening or softening due to varying load conditions.
Here’s why true stress matters:
- **Fatigue Failure:** True stress helps predict fatigue failures. It allows engineers to account for repetitive loading, which can lead to cracks in the material.
- **Creep and Creep Rupture:** This phenomenon is crucial in materials behaving under constant loads over time. True stress helps us understand how these processes affect their behavior.
- **Fracture Mechanics:** True stress plays a key role in fracture mechanics, where it helps analyze cracks and predict when they might break.
By incorporating true stress calculations into design, engineers can build more robust structures that are less prone to failure under different kinds of loads.
The Big Picture: From Engineering To Real Life
The relationship between true stress and engineering stress is vital in various branches of engineering, including civil, structural, mechanical, aerospace, biomedical, chemical, and materials science.
In simpler terms, it’s about getting to the “heart” of how a material behaves under pressure. Engineering stress helps determine load limits for a given structure, while true stress provides a more accurate understanding of that load’s impact on the material throughout its entire history under the influence of forces.
This difference allows engineers to predict and prevent failures by designing structures with greater resistance to stresses.
In this way, true stress helps bridge the gap between theoretical knowledge and practical engineering applications.